The autopilot interaction with the aircraft’s trim system is a gray area for many pilots. You can easily overpower the autopilot, but overcoming the trim that the autopilot may have run to the stop is another matter. This article will give you background information on how the autopilot trim works, a trim runaway, and how the autopilot can also slowly run the trim to the stop and then disengage.
Pitch Trim
In addition to the standard pitch, roll, and yaw servos, most modern autopilots have an optional pitch trim servo. Let’s dig into autopilot-controlled pitch trim, also called autotrim. The trim servo complements the autopilot, which is why the option is so popular. With the trim option, you can fly hands-off from climb out to short final. You don’t have to be continuously trimming the aircraft for the autopilot. Without the trim servo, it’s as if George in the right seat is flying, but you are controlling the trim from the left seat, which is not a good solution. All autopilots for turbine business aircraft, and most higher-performance piston aircraft today, have autopilot pitch trim.
Why Have a Trim Servo?
What is the purpose of the pitch trim servo? It serves the same function as handling the trim manually; it relieves the force held by the pitch (elevator) servo. Why does that matter? The pitch servo is limited in how much force it can apply to the elevator and how long it can apply that force. You could imagine the effect of a pitch servo that could abruptly use enough force to pull the yoke fully forward or aft. If done above maneuvering speed, the abrupt movement could overstress the aircraft.
Because of this, the FAA has set autopilot certification limits such that a single failure, like a pitch servo “hard-over,” will not cause a catastrophic airframe failure. During normal operation, the autopilot will command the pitch servo to pull on the elevator cable. If the force is constant in one direction for several seconds, the trim servo will activate to reduce the pitch servo force to near zero. The engineers must make tradeoffs to get the activation time delay, and trim speed dialed in. Too little delay or too fast a trim speed can lead to “trim oscillations” and porpoising.
Also, the certification requirements specify a three-second time for the pilot to recognize a problem and take action. Therefore, the designers usually provide at least a three-second delay before the trim starts, so you don’t have to fight the autopilot and trim forces in case of failure. This recognition time is reduced to one second in the approach phase.
Some aircraft like the Cirrus and Huskey don’t use aerodynamic trim but use a spring or bungee to relieve force on the stick. In either case, aerodynamic trim or spring assist, the autopilot needs the trim servo to augment its lack of stick force.
The FAA has allowed systems that are “fault-tolerant,” “fail safe,” or have automatic detection of runaway conditions to operate the trim faster than in yesteryear. What’s fail safe? A system that requires multiple failures before something bad happens normally qualifies. The introduction of digital autopilots in the 1980s has permitted these fault-tolerant designs and, consequently, faster autotrim speeds to better match the avionics and airframe requirements. Additionally, most modern autotrim systems will vary the trim speed inversely with airspeed. In other words, a slower trim speed at cruise than on climb out or approach.
Why Is It Doing That?
While the pitch trim option complements the autopilot, it also introduces another factor when it fails. The system dramatically reduces the physical workload when functioning correctly, but when it misbehaves, it suddenly increases your mental workload. There have been at least two commuter airline accidents where the autotrim was operating correctly, but the flight crews didn’t recognize what was happening. Two of these accidents were in icing conditions where the flight crew had selected altitude hold, and the autopilot kept slowly pitching up (and trimming up) due to the ice reducing the lift from the wing. The flight crew missed the decaying airspeed until there was a stall warning, and the autopilot automatically disengaged. The disengagement left the flight crew to take over manually and regain control of an aircraft trimmed almost full nose up. Both accidents were fatal.
Another incident occurred in the UK with a pilot using vertical speed in an extended climb. The same type of thing happened. The autopilot kept pitching up and trimming the nose to maintain the vertical speed while the airspeed was decreasing. The aircraft stalled, and the resulting recovery overstressed the airframe to an unsalvageable condition, but the occupants survived. In each of those cases, the system was operating normally.
What are the cases where autotrim fails? It can simply fail to trim, which is a benign failure (inconvenient rather than life-threatening), or it can run the trim continuously, called “trim runaway.” The command for the autopilot trim is from a measurement of the force the primary servo is exerting on the control cable. Failure in the sensing circuit is the usual cause of a trim runaway. If this sensing circuit thinks the pitch servo is exerting a force on the cable, the trim command will run until the force is reduced below a set threshold. Since the sensing circuit has failed it will appear to the trim system that the force is not being reduced, so the trim continues to run.
Trim runaway can happen in either direction. The recent Garmin GFC 500 Service Alert regarding the autopilot trim stated: “An uncommanded automatic pitch trim runaway may occur when the autopilot is first engaged.” While I have no inside information on this situation, when digital autopilots are first engaged, the computer must initialize (set to zero or synch to the present value) many variables in memory. Just guessing here, but maybe the servo force reading in memory was not initialized right, or there was a miscommunication with the servo. In any case, Garmin issued a software fix to resolve the situation.
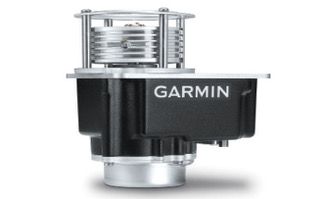
Don’t Fight It
However, another “trim failure” has affected many pilots. Remember that the trim is activated when the sensing circuit detects a servo force that lasts more than a few seconds. Most autopilots have servos containing a Direct Current (DC) motor that operates at 12 or 24 volts. The servo motor will run forward or reverse depending on the polarity. The force the servo exerts on the control surface is detected by measuring the amount of current being drawn. Typically, there will also be a current limiter to derate the motor’s full power.
So, what is this other trim failure? It’s a failure caused by pilot error when they try to overpower an engaged autopilot to take control of the aircraft. Normally the autopilot servo force is against the aerodynamic pressure on the control surface—here, the elevator. The circuit detects the current and its polarity and activates the trim. However, the pilot can overpower the servo, which causes the circuit to detect current generated not by the autopilot servo driving against aerodynamic forces but by the servo driving against the pilot’s pressure on the yoke. Since the pilot is overpowering the servo motor, the polarity of the trim opposite—if you pull back on the yoke, the autopilot will trim nose down.
You can’t have two pilots (the PIC and the autopilot) fighting over who controls the plane—it never ends well. If you as PIC want to take control, disengage the autopilot, and take control yourself or use Control Wheel Steering (CWS) for temporary manual adjustments. Never overpower an engaged autopilot while airborne. If you do, you will find it easy to overpower the autopilot servo motor initially because its power is limited, but as soon as the trim starts to come in, the more and more difficult it becomes. This is because you now must overcome the servo motor force plus the aerodynamic force on the control surface with increasing trim opposite your input. Handling an aircraft whose trim has been run to the stop is very difficult to recover when the autopilot disengages. It is startling if you disengage yourself but even more alarming if the autopilot’s logic independently decides it is time to disengage.
Editor Frank Bowlin and I both experienced this type of pilot-induced “trim failure.” Both happened on approaches. In Frank’s case, it was on an autopilot coupled ILS approach where the pilot (not Frank) wanted to stay just a bit high on the glideslope, so he held it there while coupled. When he got to the flare, the nose-down trim was startling and responsible for a far-less-than-graceful landing. (Post analysis showed the autopilot detected the force from the yoke and kept slowly trimming down. The pilot failed to recognize the excessive nose-down trim until he disengaged to land.)
My case was less spectacular, but it generated what I called an AP/PIO (Autopilot/Pilot Induced Oscillation). I was demonstrating a coupled ILS approach to a new customer. He thought the glideslope tracking could have been tighter, so he decided to help it by entering “corrections” via the yoke. After a few seconds, the trim came into play and then a few seconds later, the pilot’s inputs got out of sync with the autopilot, and it was off to the races on a wild roller-coaster ride. It went well beyond what we would call an “unstable approach”! Thankfully both Frank and I and both aircraft survived with nothing more than a cautionary story.
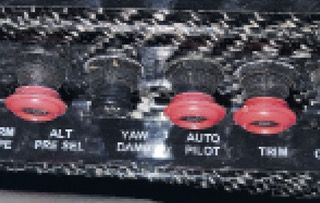
Left: In the event of a trim runaway, can you identify and pull the correct circuit breaker in a hurry? A collar could help.
Trim Indication
How do you guard against these kinds trim failures? The most important item is to monitor the trim indicator and note any unusual movement. Aircraft manufacturers have used different techniques to alert the pilot that the autotrim is operating. Boeing sets the unofficial standards for many aircraft manufacturers; on Boeing aircraft, you can see the manual (stab) trim wheel moving. Most aircraft with manual trim wheels operate similarly.
The all-electric trim systems are the hardest to monitor. Dassault has an audible “clacker” whenever the trim is in motion. Whatever your aircraft, you must know the warning signs of a trim runaway. You should know how to quickly disable the trim system blindfolded; putting collars on the circuit breakers for the autopilot and trim system can be an essential aid.
You can easily check the autotrim activation/indication by doing a simple pre-flight check per some AFM Supplements. Select a vertical mode like VS, engage the AP, and pull on the yoke. After a few seconds, the trim will start to move nose down. It will continue trimming until you release the pressure on the yoke or the trim runs to the stop. Now push on the yoke and check that the trim servo drives to a nose-up position.
As mentioned previously, you will probably be surprised that the autopilot pitch servo can be overpowered with less force than you expected; however, the out-of-trim forces make it challenging to overpower in flight. This would also be a good time to check the various ways of disengaging the autopilot and trim servo. Be sure to recenter the trim before the next flight to avoid surprises on takeoff.
Bob Teter is a retired CFI and was fortunate to have been involved in developing a wide range of avionics products, from autothrottles to weather radars. While his day job was avionics development, his off hours were spent flying, but autopilots were outside of his budget and manual electric trim was a luxury.